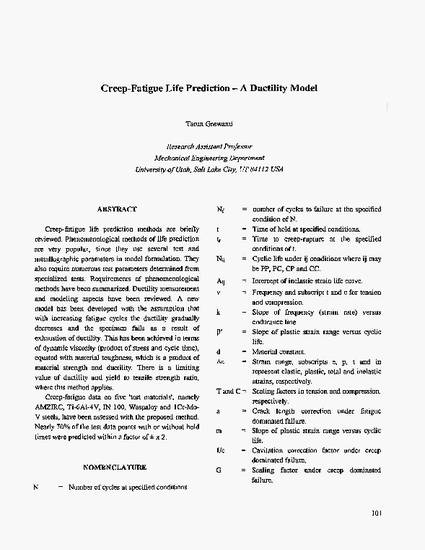
Creep-fatigue life prediction methods are briefly reviewed. Phenomenological methods of life prediction are very popular, since they use several test and metallographic parameters in model formulation. They also require numerous test parameters determined from specialized tests. Requirements of phenomenological methods have been summarized. Ductility measurement and modeling aspects have been reviewed. A new model has been developed with the assumption that with increasing fatigue cycles the ductility gradually decreases and the specimen fails as a result of exhaustion of ductility. This has been achieved in terms of dynamic viscosity (product of stress and cycle time), equated with material toughness, which is a product of material strength and ductility. There is a limiting value of ductility and yield to tensile strength ratio, where this method applies. Creep-fatigue data on five 'test materials', namely AMZIRC, Ti-6A1-4V, IN 100, Waspaloy and lCr-Mo- V steels, have been assessed with the proposed method. Nearly 70% of the test data points with or without hold times were predicted within a factor of ± χ 2.
Available at: http://works.bepress.com/tarun-goswami/39/
This work is licensed under a Creative Commons Attribution-NonCommercial-NoDerivs 3.0 Unported License.