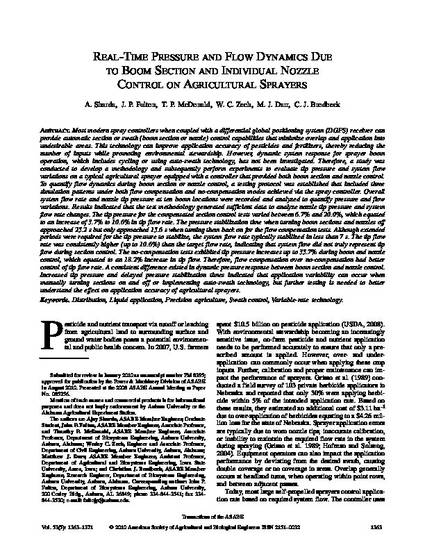
Most modern spray controllers when coupled with a differential global positioning system (DGPS) receiver can provide automatic section or swath (boom section or nozzle) control capabilities that minimize overlap and application into undesirable areas. This technology can improve application accuracy of pesticides and fertilizers, thereby reducing the number of inputs while promoting environmental stewardship. However, dynamic system response for sprayer boom operation, which includes cycling or using auto-swath technology, has not been investigated. Therefore, a study was conducted to develop a methodology and subsequently perform experiments to evaluate tip pressure and system flow variations on a typical agricultural sprayer equipped with a controller that provided both boom section and nozzle control. To quantify flow dynamics during boom section or nozzle control, a testing protocol was established that included three simulation patterns under both flow compensation and no-compensation modes achieved via the spray controller. Overall system flow rate and nozzle tip pressure at ten boom locations were recorded and analyzed to quantify pressure and flow variations. Results indicated that the test methodology generated sufficient data to analyze nozzle tip pressure and system flow rate changes. The tip pressure for the compensated section control tests varied between 6.7% and 20.0%, which equated to an increase of 3.7% to 10.6% in tip flow rate. The pressure stabilization time when turning boom sections and nozzles off approached 25.2 s but only approached 15.6 s when turning them back on for the flow compensation tests. Although extended periods were required for the tip pressure to stabilize, the system flow rate typically stabilized in less than 7 s. The tip flow rate was consistently higher (up to 10.6%) than the target flow rate, indicating that system flow did not truly represent tip flow during section control. The no-compensation tests exhibited tip pressure increases up to 35.7% during boom and nozzle control, which equated to an 18.2% increase in tip flow. Therefore, flow compensation over no-compensation had better control of tip flow rate. A consistent difference existed in dynamic pressure response between boom section and nozzle control. Increased tip pressure and delayed pressure stabilization times indicated that application variability can occur when manually turning sections on and off or implementing auto-swath technology, but further testing is needed to better understand the effect on application accuracy of agricultural sprayers.
Available at: http://works.bepress.com/matthew_darr/27/
This article is from Transactions of the ASABE 53, no. 5 (2010): 1363–1371.