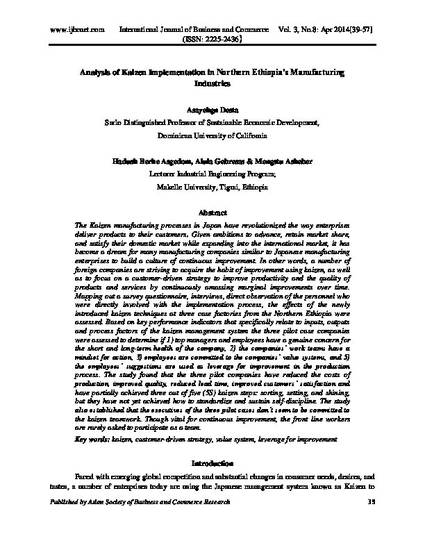
The Kaizen manufacturing processes in Japan have revolutionized the way enterprises deliver products to their customers. Given ambitions to advance, retain market share, and satisfy their domestic market while expanding into the international market, it has become a dream for many manufacturing companies similar to Japanese manufacturing enterprises to build a culture of continuous improvement. In other words, a number of foreign companies are striving to acquire the habit of improvement using kaizen, as well as to focus on a customer-driven strategy to improve productivity and the quality of products and services by continuously amassing marginal improvements over time. Mapping out a survey questionnaire, interviews, direct observation of the personnel who were directly involved with the implementation process, the effects of the newly introduced kaizen techniques at three case factories from the Northern Ethiopia were assessed. Based on key performance indicators that specifically relate to inputs, outputs and process factors of the kaizen management system the three pilot case companies were assessed to determine if 1) top managers and employees have a genuine concern for the short and long-term health of the company, 2) the companies’ work teams have a mindset for action, 3) employees are committed to the companies’ value systems, and 5) the employees’ suggestions are used as leverage for improvement in the production process. The study found that the three pilot companies have reduced the costs of production, improved quality, reduced lead time, improved customers’ satisfaction and have partially achieved three out of five (5S) kaizen steps: sorting, setting, and shining, but they have not yet achieved how to standardize and sustain self-discipline. The study also established that the executives of the three pilot cases don’t seem to be committed to the kaizen teamwork. Though vital for continuous improvement, the front line workers are rarely asked to participate as a team.
Available at: http://works.bepress.com/asayehgn_desta/43/